Painting systems
The following pages provide guidance on paint systems suitable for use in industrial and commercial situations under six different “service requirements” as follows:
Service Requirement
1 | Low corrosivity conditions & medium term service |
2 | Low corrosivity conditions and high resistance to wear and trafficking/long term service. |
3 | Medium corrosivity conditions and high resistance to wear and trafficking/long term service. |
4 | High corrosivity conditions and high resistance to wear and trafficking/long term service. |
5 | Very high corrosivity conditions and high resistance to wear and trafficking/long term service. |
6 | Specific industrial chemical or solvent exposure. |
Notes
- Service life: The paint systems listed in this guide provide for either medium or long term service lives, which are typically 5 to 10 years or 10 to 15 years respectively, for a maintenance repainting cycle to retain aesthetic performance.
- The atmospheric corrosivity condition assessment is based upon AS 4312, which provides excellent guidance for the determination of the general Australian macro environment with respect to corrosivity zones and the guidelines of AS/NZS 2312.2, which essentially defines corrosivity in terms of distance from the seacoast. “Corrosivity Environment – A Quick Guide” (page 14) provides assistance on choosing the corrosivity environment.
NOTE: AS/NZS 2312.2 – 2014 includes the new extreme (CX) corrosivity zone. The GAA has no paint system recommendation for category CX at the time of preparation of this guide. - Application should be strictly in accordance with the paint manufacturer’s written instructions and the relevant recommendations of AS/NZS 2311 in the case of Service Requirement 1 and to AS/NZS 2312.2 in the case of Service Requirements 2 to 6.
- For all but Very Low and Low Corrosivity Service Requirements it is recommended that a brush applied stripe coat be applied to corners, welds and other sharp edges to ensure full thickness coverage. Indeed, for High and Very High Corrosivity Conditions it is critical. This is because, unlike hot dip galvanizing, paint tends to shrink away from sharp edges.
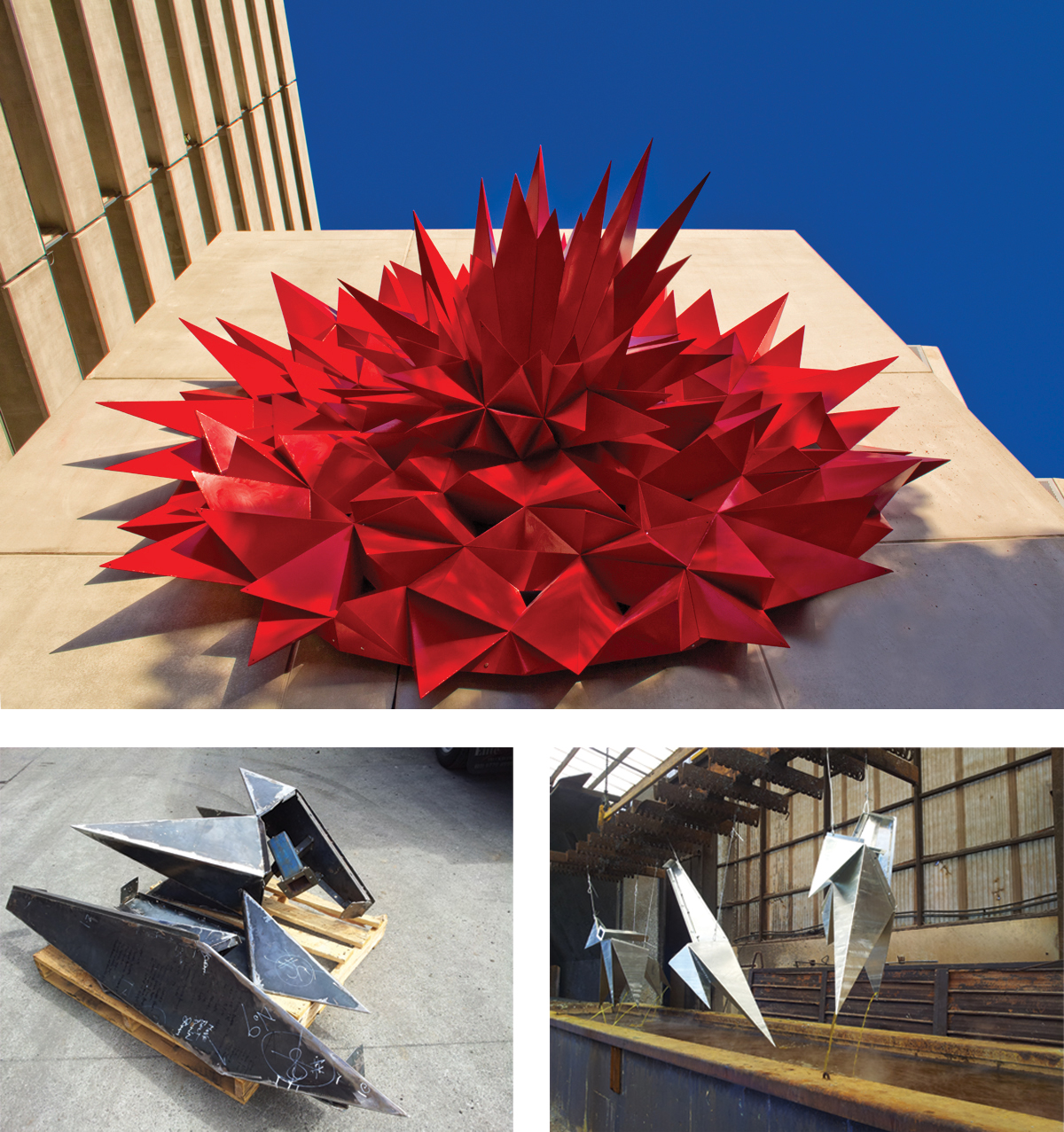
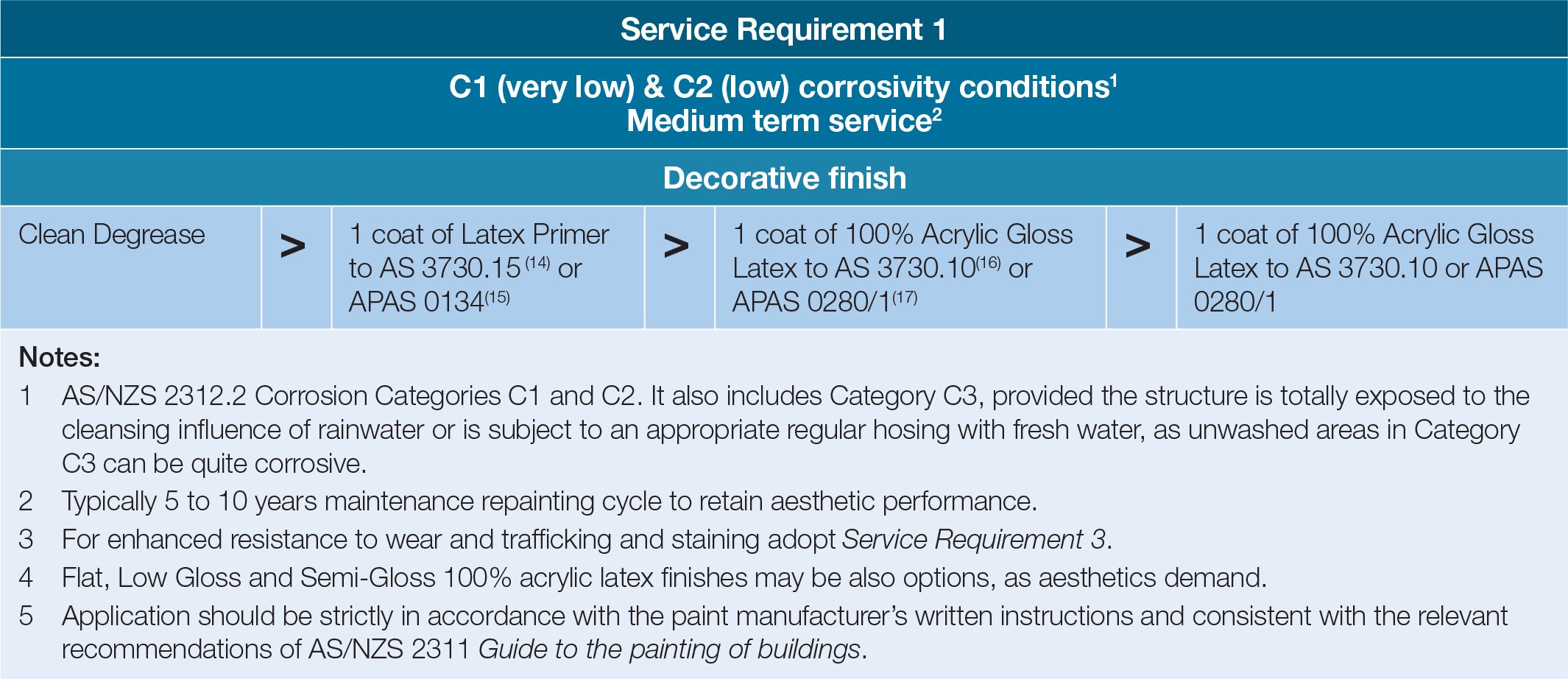
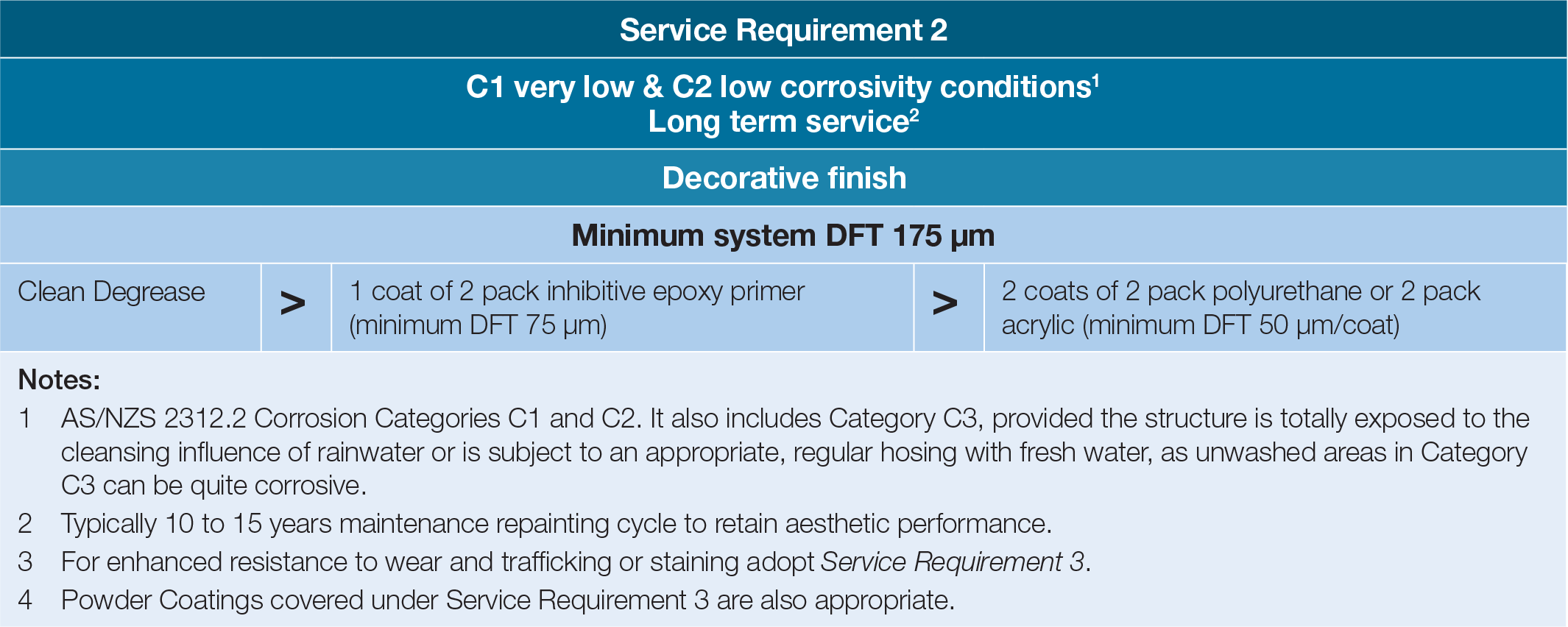
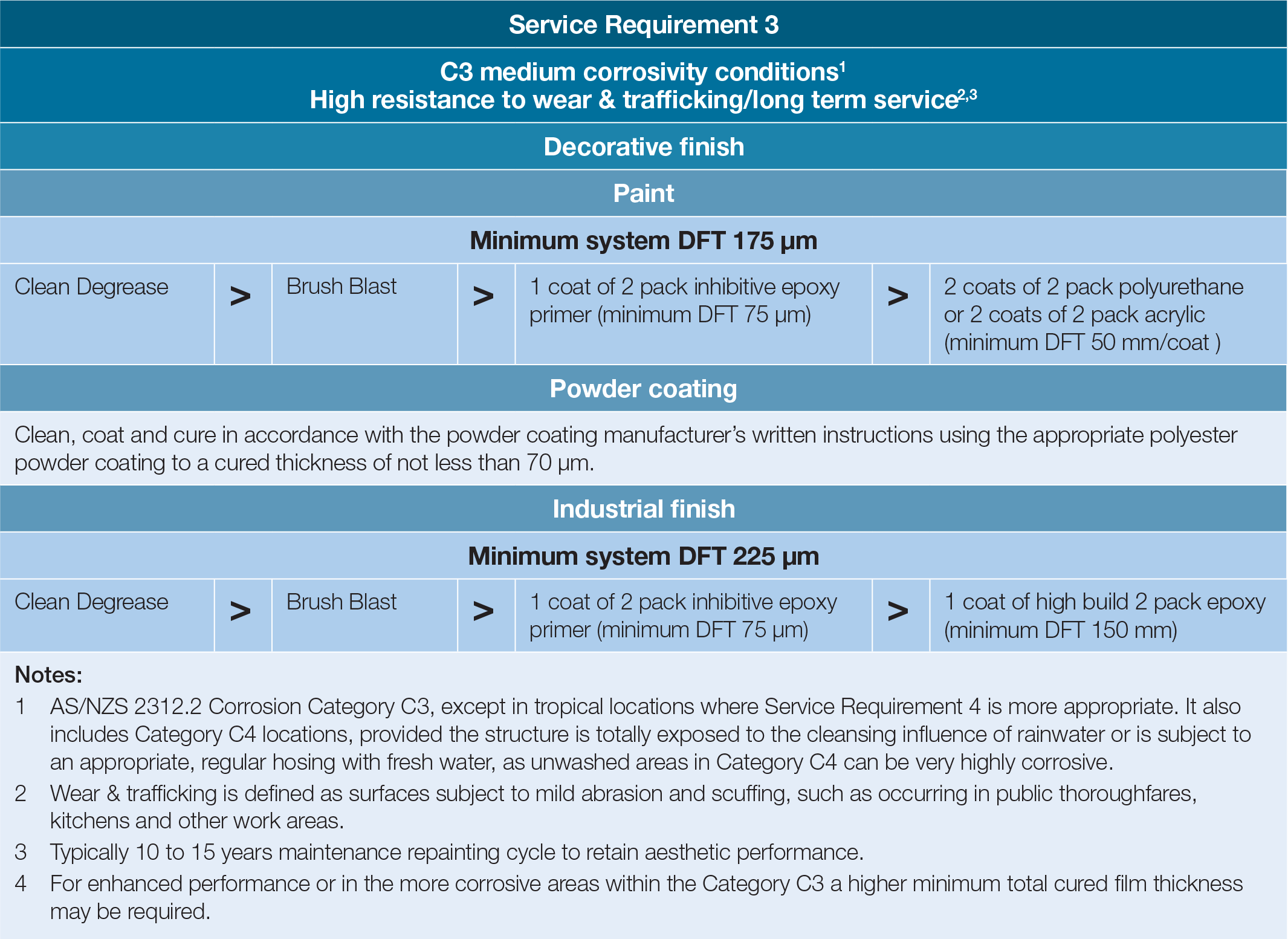

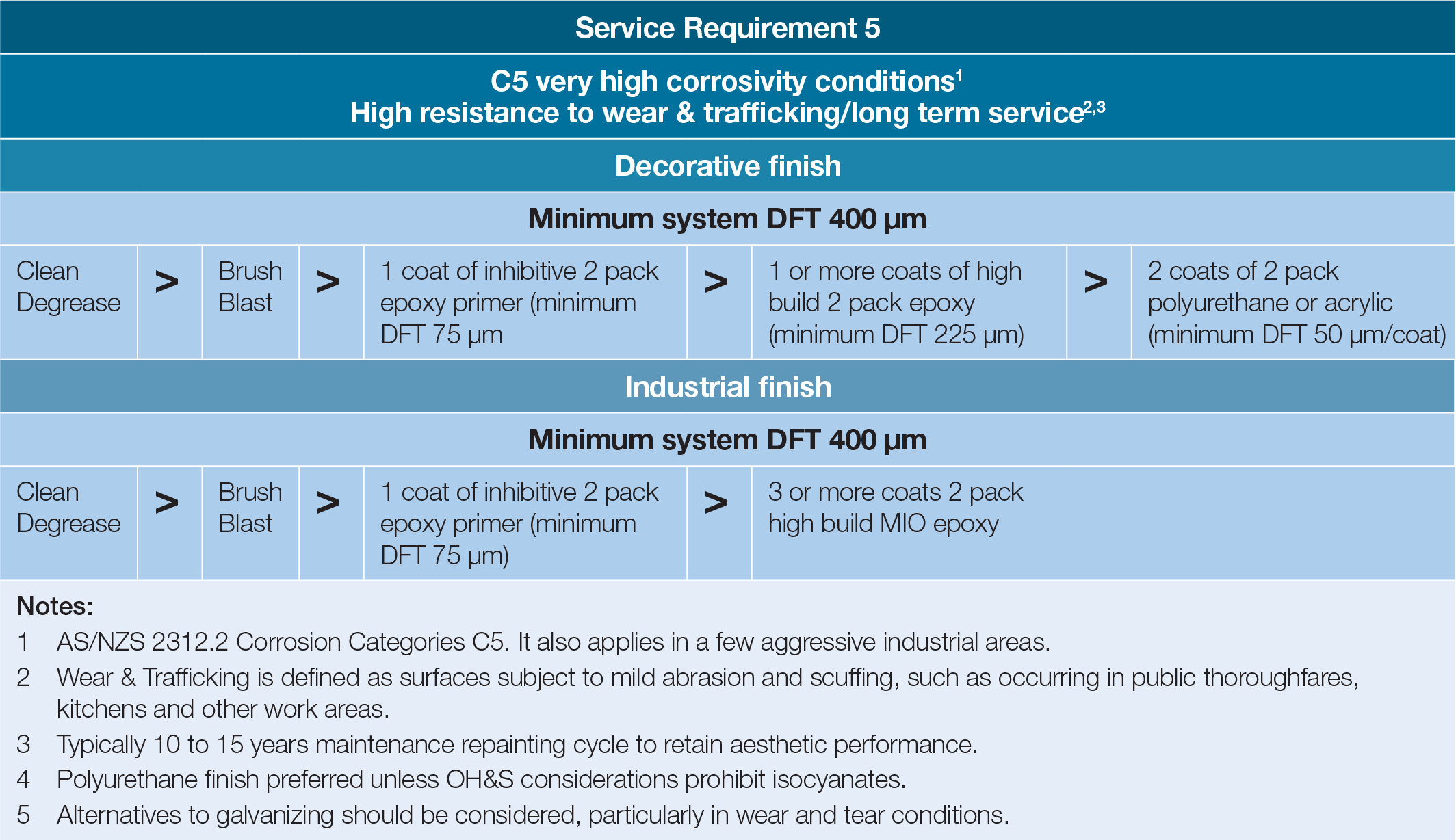
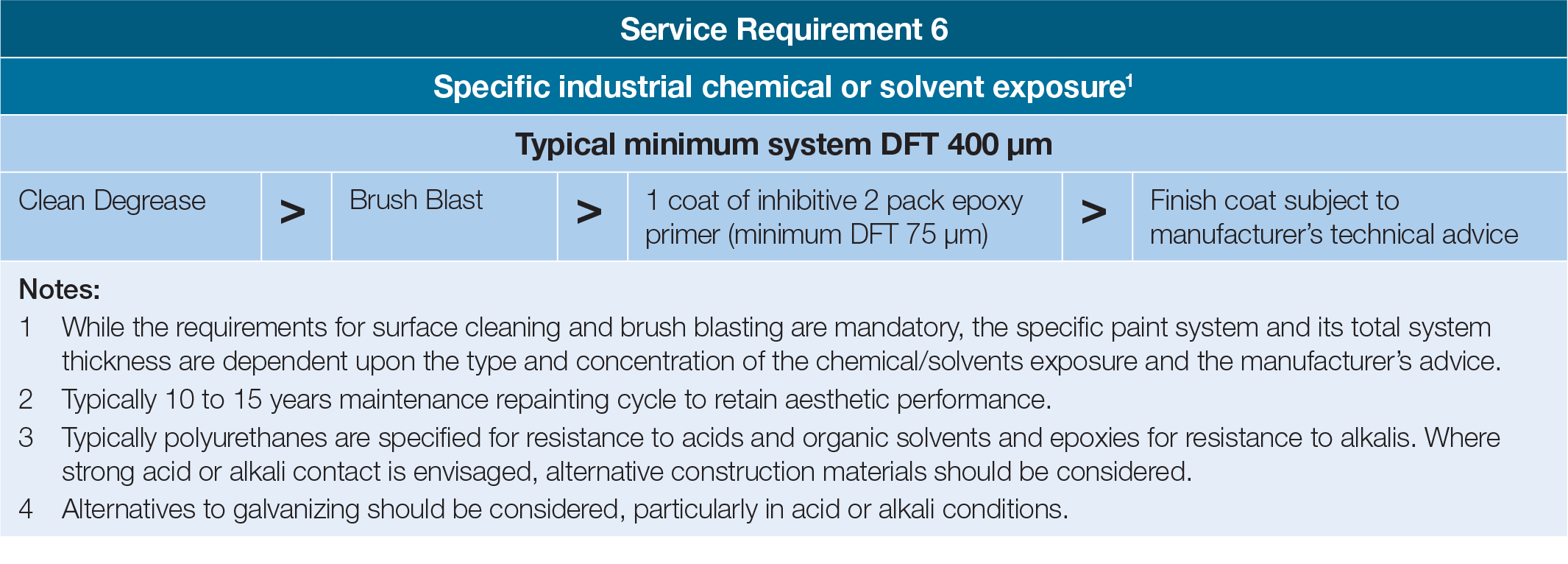